Injection moulding of plastics is one of the most widely used production techniques to create high precision plastic components in large volumes. This technology enables the production of complex shapes, with reduced production times and optimised costs, making it an ideal solution for a wide range of industrial sectors.
In over 20 years of plastic moulding experience we have acquired the technical expertise to understand application requirements in every sector, and are able to meet these requirements with effective solutions.
We collaborate with mould manufacturers and producers and can carry out the following:
- injection moulding
- blow moulding
- double injection moulding
- dual-material moulding
Our production cycle is implemented using 19 injection moulding machines (Arburg and Fanuc) for single and dual-material parts, which operate 24 hours a day, 7 days a week. Furthermore, we always have 2 moulding machines at 50% load to fulfil urgent requirements within 24 hours.
After the production phase we can handle product packaging and post-production operations in our dedicated department, entrusting silk-screen printing, laser processing, chrome-plating, welding or pad printing operations to authorised expert suppliers.
Browse the application areas
Strengths and services
In Teksae, we deal with plastic molding with an approach focused on quality, innovation and customization. Our goal is to provide products that fully meet the needs of our customers, ensuring reliability and durability.
Our strengths are:
Customization: we work closely with customers to develop customized solutions, based on the specific needs of the project.
Wide range of materials: we offer a selection of high quality polymers, which guarantee excellent performance in all conditions of use.
Technological innovation: we use advanced machinery and quality control systems to monitor every stage of production, ensuring flawless results.
Sustainability: we are committed to minimising our environmental impact, using recyclable materials and energy-efficient processes.
Fields of application
Our plastic moulding service is versatile and has applications in different sectors:
Automotive: manufacture of high precision, durable vehicle components.
Electronics: lightweight but durable parts for electronic devices.
Medical: production of safe, hygienic and standard-compliant devices and instruments.
Food: we have implemented the production of components with Food- M.O.C.A.
Cosmetics: we produce caps, components and packaging for the cosmetics sector.
Automation: for the field of automation we produce all components according to design that a machine may need
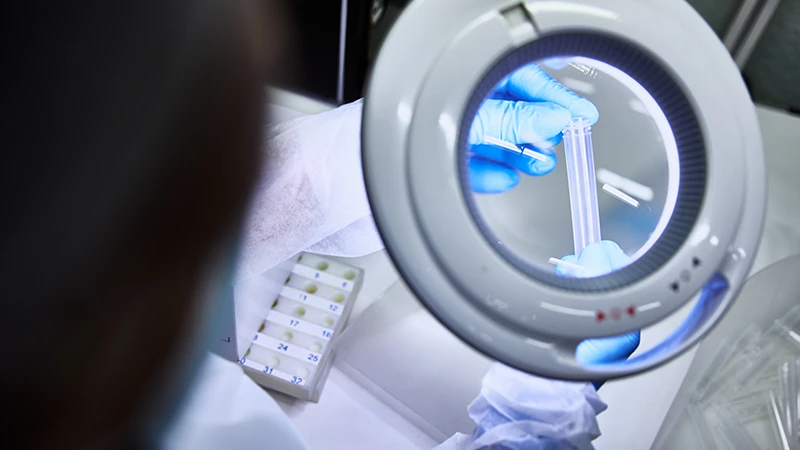
Plastic moulding for medical
For the medical sector we produce tubes with internally assembled caps and diagnostic material. We are ISO 13485 certified and regularly sanitise our production department to ensure a healthy environment, where we produce items according to medical standards.
Medical plastics molding is a key technology in the healthcare industry, enabling the production of essential medical devices for diagnosis, treatment and patient care.
One of the main considerations in medical plastics molding is the choice of appropriate materials. The plastic resins used must comply with medical standards and regulations, ensuring the safety and effectiveness of the devices produced.
Commonly used materials include polypropylene (PP), polyester (PET), polycarbonate (PC) and polyethylene (PE), which are known for their chemical resistance, biocompatibility and sterilization properties.
Medical plastics molding also offers greater flexibility in the design and customization of medical devices. This technology allows for the production of complex components with precise geometries, allowing better adaptability to the specific requirements of patients and healthcare professionals.
From a regulatory perspective, medical plastics molding must comply with stringent health sector standards and regulatory requirements such as the ISO 13485 certification for the quality management system of medical devices. It is essential to ensure the traceability of materials used, equipment and production processes in order to meet the required safety and legality standards.
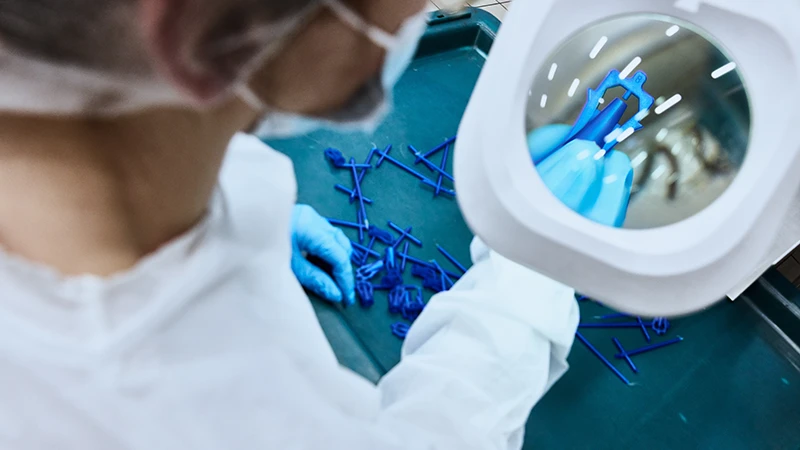
Plastic moulding for electromedical
We produce valves and seals for medical equipment, including some components of operating room instruments, oxygen mask components and aerosol ampoules.
Electromedical plastics molding plays a crucial role in the electromedical industry, enabling the production of essential devices used for diagnosis, monitoring and treatment of patients.
Chemical resistance is a crucial aspect in the moulding of electro medical plastics. Medical devices may be exposed to aggressive chemicals, such as disinfectants or cleaning solutions, which could impair the electrical and mechanical properties of materials. It is essential to select plastic resins that can resist such chemical agents without degrading or losing their insulating and electrical conductivity properties.
Another key factor in the moulding of electro medical plastics is electrical safety. Medical devices shall be designed and manufactured in accordance with electrical safety standards, such as IEC 60601. This involves the use of appropriate insulating materials that meet the dielectric strength and electrical insulation requirements to protect patients and medical workers from electrical hazards.
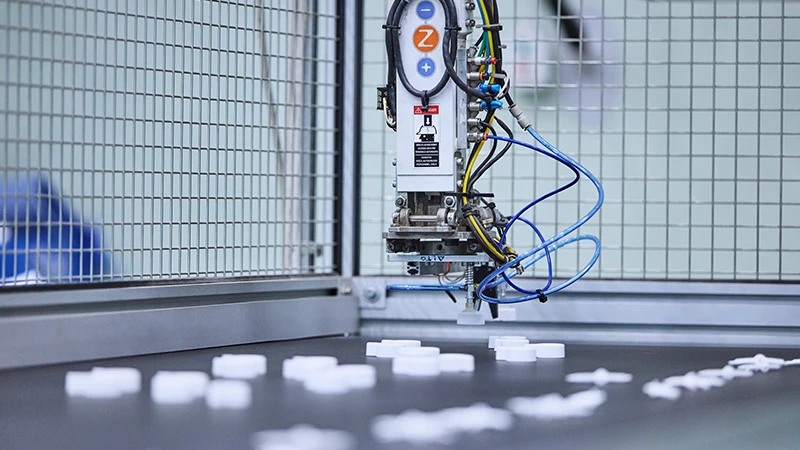
Plastic moulding food
We have implemented the production of components with Food- M.O.C.A. requirements and we produce containers, packaging and components suitable for contact with food, bottle caps and plastic parts intended for professional coffee machines.
The moulding of food-grade plastics is a fundamental process for the production of containers, packaging and tools used in the food industry. This technology allows to create safe, hygienic and compliant products, ensuring the protection and preservation of food.
One of the main considerations in food plastic molding is the choice of materials. It is essential to use approved and certified plastic resins for contact with food, which comply with the regulations and regulations specific to the countries where the products will be marketed.
During the process of molding food plastics, it is important to ensure the cleanliness and hygiene of the molds and equipment used. Mould surfaces must be smooth, non-porous and easy to clean to prevent the growth of bacteria or contaminants. It is essential to follow strict cleaning and sterilization procedures to ensure compliance with food safety regulations and the prevention of possible health risks for consumers. The moulding of food-grade plastics plays a crucial role in the food industry, enabling the production of safe, hygienic and functional packaging.
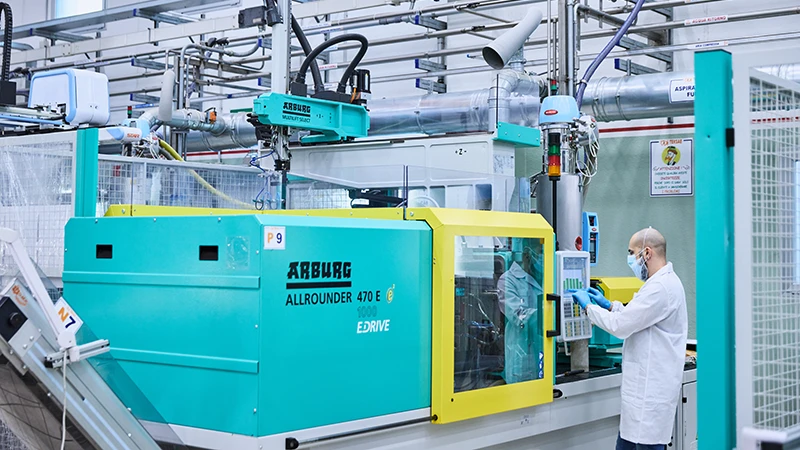
Plastic moulding for automotive
For the automation field we produce all the components a machine may need, from valves to gaskets, from plastic parts that replace metal parts to spare parts.
The moulding of automotive plastics plays a fundamental role in the production of components and parts used inside vehicles. This technology offers numerous advantages, including lightness, strength, flexible design and the possibility of integrating different functions.
The strength of plastics used in automotive plastic molding is a crucial aspect. Automotive components are subject to mechanical, thermal and environmental stresses such as vibration, extreme temperatures and chemicals in the automotive environment. Therefore, the materials used must guarantee good resistance to wear, impact, corrosion and chemical substances, maintaining their mechanical and structural properties over time.
Plastic resins can be easily shaped to fit into complex and aerodynamic designs, allowing the construction of components that meet the aesthetic and functional requirements of modern vehicles. In addition, the possibility of integrating different functions into a single component such as lighting systems, sensors or ventilation ducts allows space to be optimised and the assembly of vehicles to be simplified.
Quality and safety are key factors in the moulding of automotive plastics. Automotive components must comply with safety standards and undergo rigorous quality controls to ensure their reliability and durability.
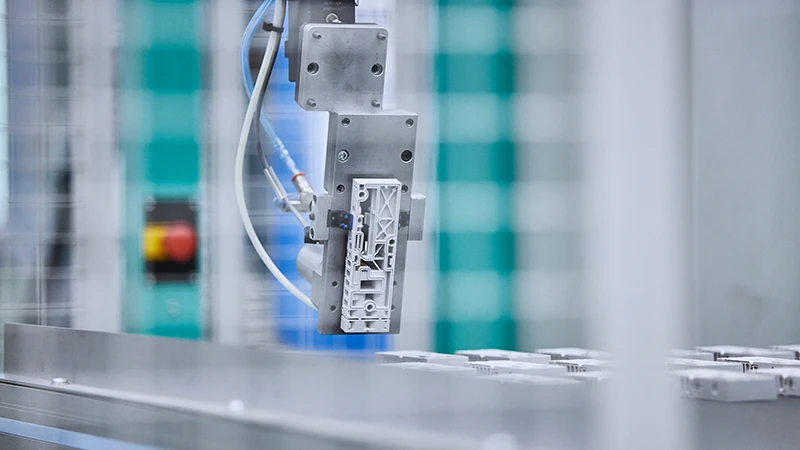
Plastic moulding for automation
For the automation field we produce all the components a machine may need, from valves to gaskets, from plastic parts that replace metal parts to spare parts.
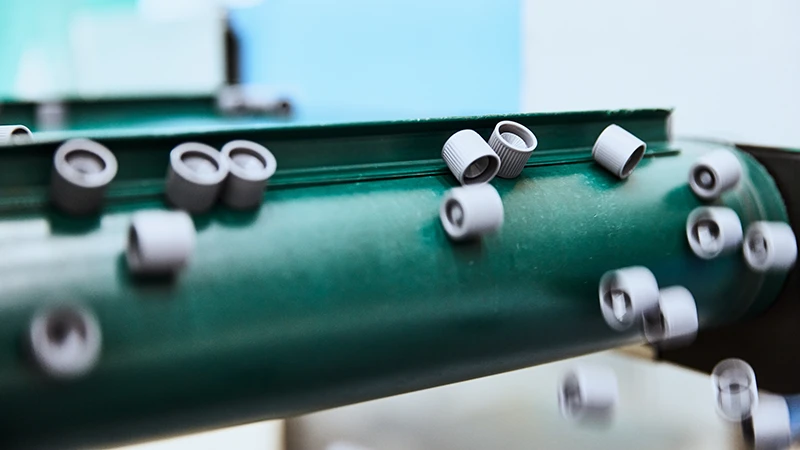
Plastic moulding for cosmetics
For the cosmetics sector we produce caps, components and packaging.
Plastic molding for cosmetics is the fundamental technology for the cosmetic industry to produce packaging and containers for cosmetic products.
Commonly used materials include POLYPROPYLENE( PP), POLYESTER( PET), COPOLYESTER (PETG-PCTG-PCTA) and recycled materials such as RPET and GREEN such as PLA and PHA. The moulding of plastic materials for cosmetics allows to adopt green solutions by replacing many traditional plastics such as ABS and PET with innovative materials and zero impact, achieving excellent aesthetic and functional results.
Thanks to our in-house know-how and close collaboration with green materials manufacturers, we can offer customers support for the development of their new projects.